What Gebaplast does
We create unique plastic products to grow your business. Production via our injection molding machines is preceded by an entire process of consulting, thinking along, drawing, developing, making 3D samples and testing. We are also much more than just an injection molding plant. The added value is precisely in the process that precedes production. Customers contact us for a reason when they encounter challenges in their processes and they think plastic is the solution.
Our development programs are always customized
Plastic granules can be molded practically into any shape. Gebaplast has extensive machinery where the latest technology has been incorporated.
We specialize in custom projects where we take on the entire development process together to create the product you want.
Advising and thinking along
For every question there is a solution. We relish the challenge of working with our customers to find the best solution.
Drawing and 3D printing
Using 3D drawings and 3D printing, we can relatively easily work out and explore all the possibilities.
Development and testing
Through continuous development and testing, we achieve the unique product that helps you grow your business.
What does a development program look like?
Using an example, we would like to take you through such a development process. The track below shows the development of the Drumclip. Drumclip is the solution to transport drums, full of chemicals for example, safely and certified throughout the distribution chain.
It always starts with a problem that customers encounter and where they often already have a (first) idea how to tackle this problem. In the case of Drumclip, it was about efficiently securing 200-liter steel drums to pallets. The drums are full of chemicals, ink, glue or food concentrates, so safety is a priority.
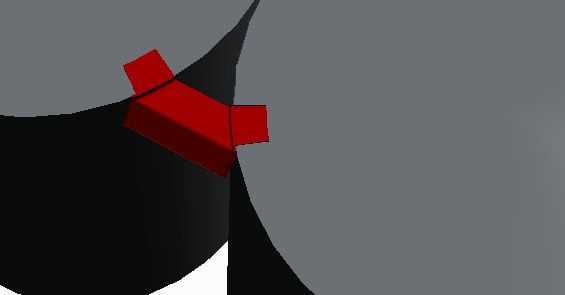
1. Thinking along and Giving Advice
There was already an idea to connect the drums with a connecting piece and to tighten a strap over them. Together with the client, Gebaplast further developed this idea and we collaborated on the final design.
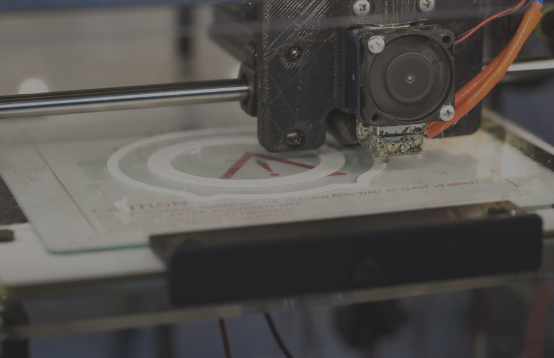
2. Design
We often make the initial sketches as early as the consulting phase, as this speeds up the creative process. The same goes for Drumclip. After we had jointly decided to go for a specific design, we continued to develop it in 3D drawings and made the first 3D prints.
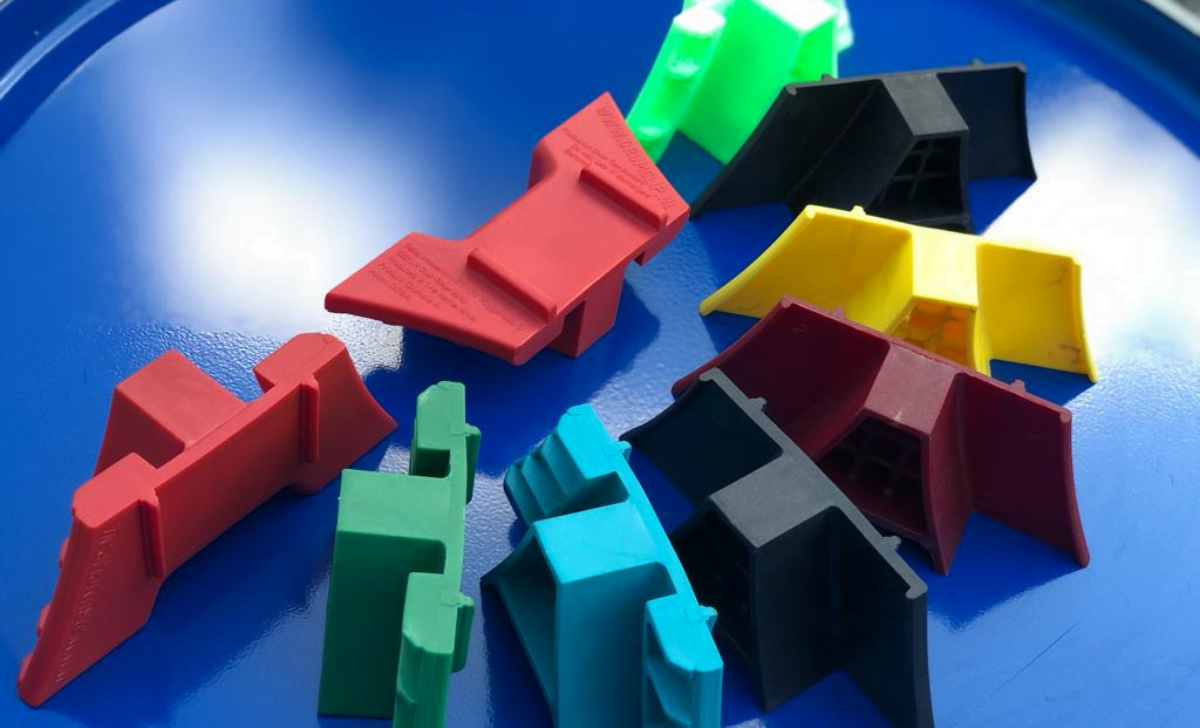
3. Testing
Because of the flow direction of the material, we had to make real molds for testing. 3D prints are made up of layers and they would break immediately in the first test. The 3D prints were good for testing the shape, though. On site, we conducted several tests to test the stiffness of the design. In the end, we did 8 tests, each time having fine-tuned the design.
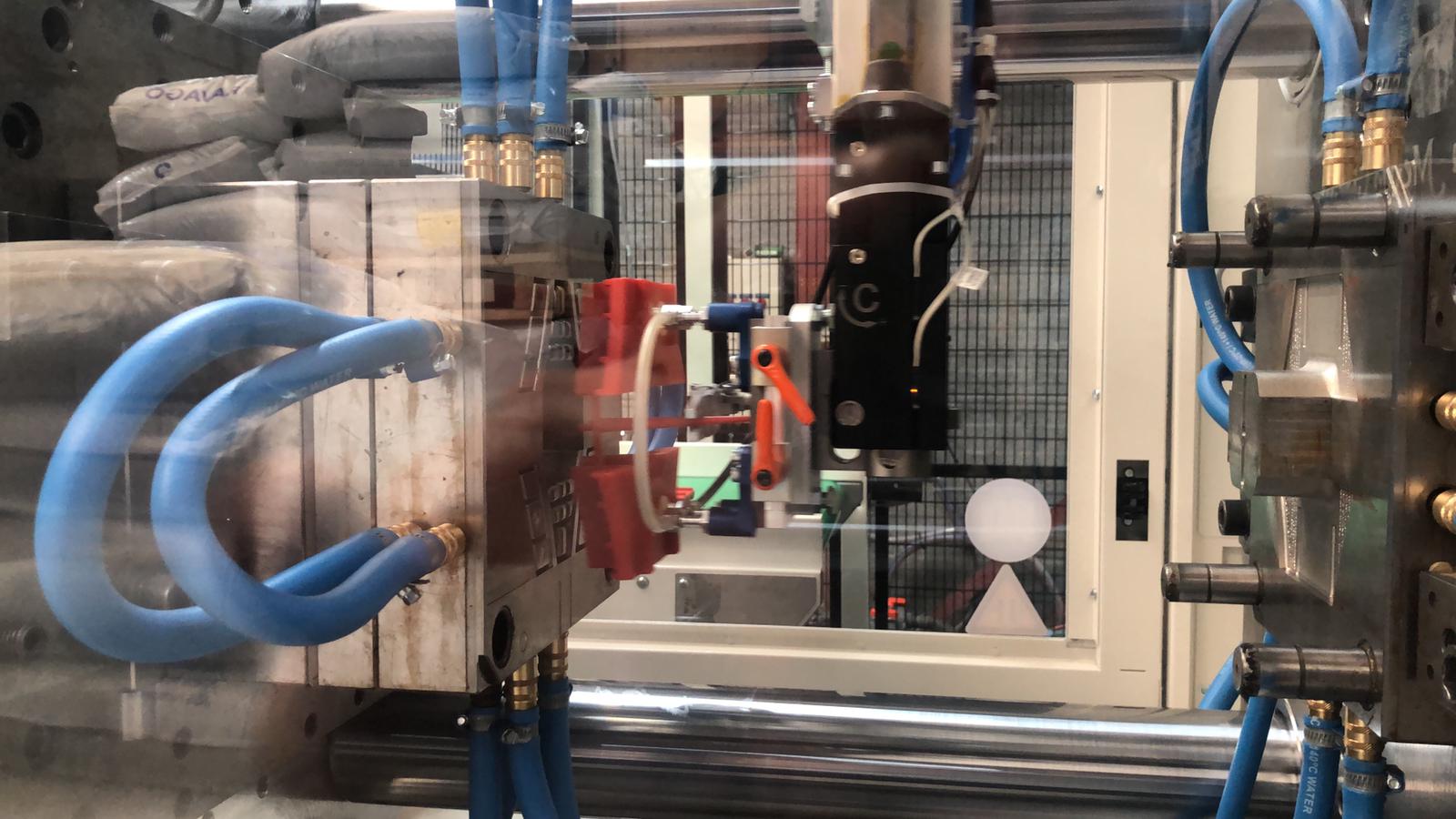
4. Produce
After the final design was approved, we made the final molds and production of the red and green Drumclip started. The Drumclip is certified to TÜV DIN-EN 12195-1, ISTA 3E Pallet Stability and EUMOS 40509, proving we have produced the right design. Thousands of drums worldwide are now transported safely and certified.
State-of-the-art machinery
What techniques do we master?
Gebaplast has extensive machinery in which the changing techniques have been anticipated. For example, take-out robots and complete automations are used to ensure flawless production processes. The production process with optimal cycle times runs 24/7. With state-of-the-art machinery, we offer the following techniques for the complete range of plastics from small to large from packaging to technical injection molding.
Injection molding
With injection molding, plastic supplied as granules or powder is melted into a viscous mass and injected under high pressure into a mold whose cavity (or cavity) is the shape of the desired product. Cooling solidifies the plastic and produces the desired product. Injection molding is one of the most widely used forming techniques for plastic parts. Injection molding allows the creation of complex products. However, due to the cost of making a mold, injection molding is only suitable for large production quantities.
3D drawing and 3D printing
A 3D printer A 3D printer is a printer that can produce three-dimensional objects based on digital construction drawings. This is done by building up the object layer by layer. Typically, 3D printers use plastic because it is cheaper and easier to use. 3D printers are mainly used where designers want to save time on making models themselves.
In Mould Labeling (IML).
In Mould Labeling (IML) is used for printing on plastic packaging and/or products. A pre-printed polypropylene label is placed in a mold. Molten polypropylene is then added into the mold. The result is that after curing, the pre-printed label is incorporated into the plastic product.
Laser marking
Laser marking of plastics is a process in which components are labeled or marked using a laser. Depending on the polymer, the method used is determined. The advantage of laser marking is that it is waterproof, abrasion-resistant and heat-resistant.
Ultrasonic welding
This welding process fuses compressed plastics by using a powerful concentrated high-frequency sound beam. The combination of pressure and sound energy is enough to vibrate the surface of the materials to the point of melting.
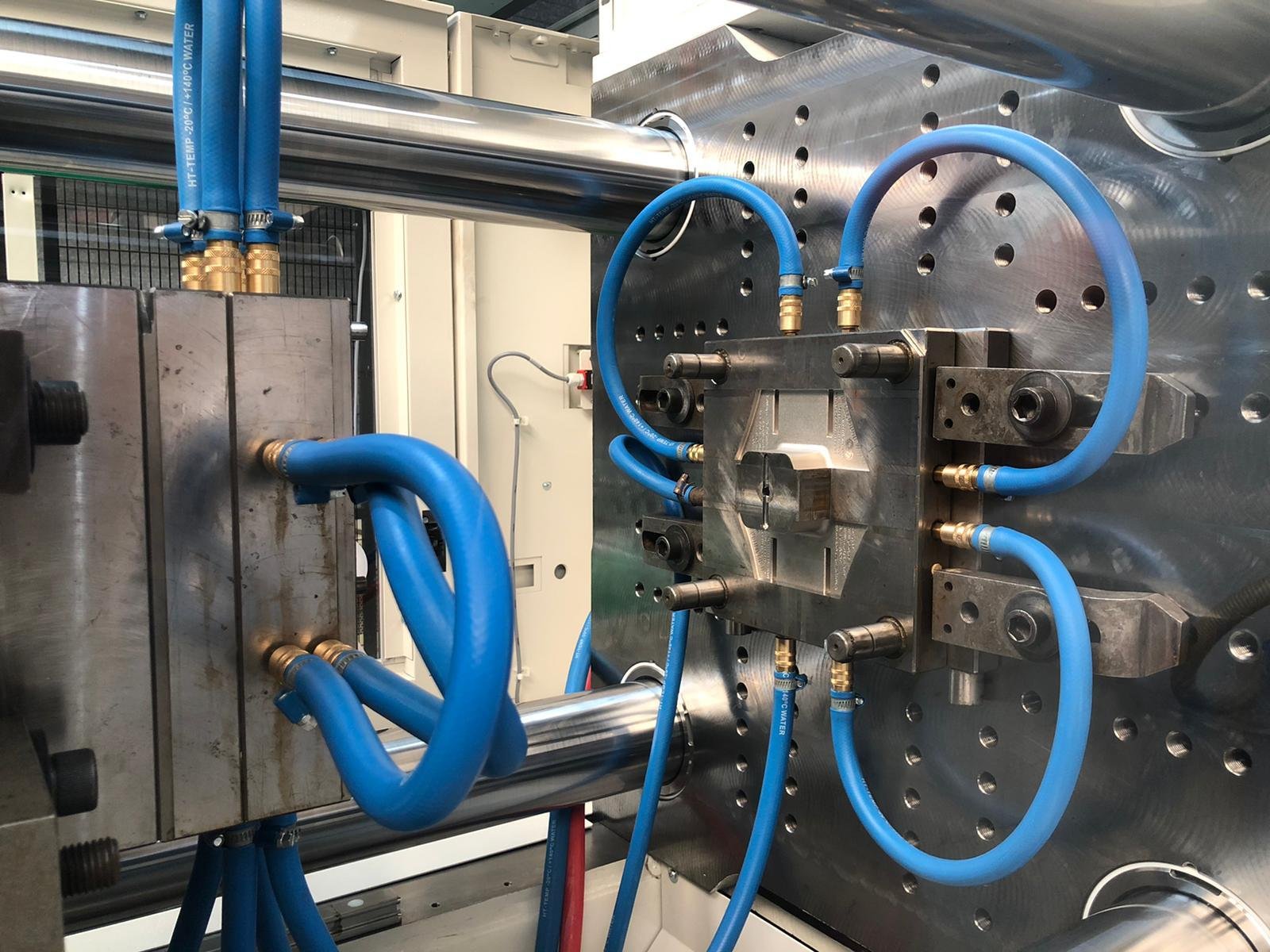